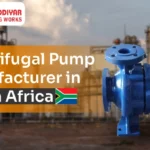
Centrifugal Pump Manufacturer in South Africa
December 11, 2024
Thermic Fluid Hot Oil Pump for Pharmaceutical Industries
January 23, 2025Introduction
Centrifugal pumps are among the most versatile and widely used industrial pumps today. These pumps operate on the principle of centrifugal force to move fluids, making them ideal for a range of industries. With their ability to handle high flow rates and provide steady, non-pulsating output, they are an essential component in various chemical processes.
In the chemical industry, pumps play a critical role in transferring liquids, handling corrosive chemicals, and ensuring smooth operations in production lines. They are indispensable for maintaining the efficiency and safety of processes, such as transporting acids, solvents, or slurries. Reliable pumps are key to avoiding downtime and costly disruptions.
Centrifugal pumps are a preferred choice for chemical industries due to their robust design, efficiency, and adaptability. For example, their ability to handle fluids with varying viscosities and temperatures makes them ideal for applications like water treatment, oil refining, and chemical synthesis. Their ease of maintenance and cost-effectiveness further add to their popularity in this sector.
In this blog, we’ll highlight the benefits of centrifugal pumps in the chemical industry and explore why they are an essential solution for complex fluid-handling challenges.
Centrifugal Pumps & it's Working Principle
Centrifugal pumps are mechanical devices designed to move fluids using rotational energy from a motor or engine. The pump impeller rotates, creating centrifugal force that pushes the fluid outward to the pump’s discharge. This simple yet effective principle makes centrifugal pumps ideal for handling large volumes of liquids in industries like chemicals. For example, they are commonly used for transferring acids and bases in manufacturing facilities.
Key Components of a Centrifugal Pump
The main components of a centrifugal pump include the impeller, casing, shaft, and mechanical seal. The impeller generates the centrifugal force, while the casing directs the flow of fluid efficiently. The shaft connects the impeller to the motor, and the seal prevents leaks during operation. Each component is engineered to ensure reliability and performance, especially when dealing with corrosive or abrasive chemicals.
Types of Centrifugal Pumps
Side suction centrifugal pumps are widely used in the chemical industry due to their straightforward design and easy installation. These pumps are efficient in handling low-viscosity fluids like water and chemical solvents, making them a practical choice for applications requiring high flow rates.
2. Closed Impeller Centrifugal PumpClosed impeller pumps are preferred for handling clean or mildly contaminated fluids. The enclosed design minimizes fluid recirculation and improves efficiency. They are commonly used in chemical processing plants for tasks such as transferring pure chemicals or solutions.
3. Semi-Open Centrifugal PumpSemi-open impeller pumps are suitable for handling liquids containing small solids or slurries. Their partially open design prevents clogging, making them ideal for chemical industry processes involving abrasive or viscous fluids. For example, they are effective in handling slurry mixtures in fertilizer manufacturing.
By understanding the definition, components, and specific types of centrifugal pumps, it’s easier to identify their suitability for different chemical industry applications.
Importance of Precision and Hygiene in Chemical Operations
Precision and hygiene are paramount in chemical industry operations to maintain product quality and safety. Centrifugal pumps are designed to deliver consistent flow and accurate dosing, reducing the risk of contamination or process inefficiencies. For example, pharmaceutical-grade centrifugal pumps are often used in chemical manufacturing to produce clean and sterile compounds. Their smooth, non-reactive surfaces ensure compliance with strict hygiene standards.
- According to industry reports, centrifugal pumps account for over 80% of all industrial pump applications worldwide, underlining their dominance in sectors like chemicals. Their efficiency and versatility make them the go-to solution for managing complex fluid-handling tasks.
Features of Centrifugal Pumps for the Chemical Industry
1. Materials Used for Chemical-Grade Pumps Centrifugal pumps designed for the chemical industry are made using high-grade materials like stainless steel, Hastelloy, and fluoropolymers. These materials offer exceptional durability and resistance to harsh chemicals. For example, stainless steel pumps are commonly used for transferring acids and caustic solutions due to their robust construction and long lifespan.
2. Corrosion Resistance and Chemical Compatibility Chemical processes often involve corrosive substances, and centrifugal pumps are engineered to withstand these challenges. With features like corrosion-resistant coatings and chemically inert materials, these pumps ensure safe and efficient handling of aggressive fluids. A case in point is their use in handling sulfuric acid in fertilizer manufacturing plants, where reliability is critical.
3. Easy Cleaning and Maintenance (CIP and SIP Systems) Centrifugal pumps equipped with Clean-In-Place (CIP) and Sterilize-In-Place (SIP) systems make maintenance seamless, especially in industries requiring stringent hygiene. These systems allow pumps to be cleaned without disassembly, reducing downtime and ensuring contamination-free operations. This is particularly beneficial in pharmaceutical chemical processes where sterility is non-negotiable.
4. Energy Efficiency and Operational Reliability Centrifugal pumps are known for their energy efficiency, with advanced models reducing energy consumption by up to 20%. Their design minimizes friction losses, ensuring smooth and consistent fluid flow. Additionally, features like wear-resistant impellers and seals enhance operational reliability, making them a preferred choice for continuous-duty applications in the chemical industry.
By combining durable materials, chemical compatibility, ease of maintenance, and energy efficiency, centrifugal pumps deliver unmatched value to the chemical industry, supporting safe and cost-effective operations.
Applications of Centrifugal Pumps in the Chemical Industry
1. Liquid Transfer and Chemical Processing Centrifugal pumps are essential for liquid transfer and chemical processing in the chemical industry. They efficiently move large volumes of fluids, such as acids, alkalis, and solvents, from storage tanks to reactors or between process stages. For instance, these pumps are widely used in the production of cleaning agents to handle corrosive raw materials with precision and safety.
2. Filtration and Separation Processes In filtration and separation processes, centrifugal pumps play a vital role by maintaining a consistent flow rate and pressure. This ensures optimal performance of filters, centrifuges, and separators. For example, in pharmaceutical chemical plants, centrifugal pumps support processes like solvent recovery by delivering the required fluid dynamics for effective separation.
3. Handling of Sensitive or Sterile Solutions Centrifugal pumps are designed to handle sensitive or sterile solutions without compromising their integrity. With smooth internal surfaces and cleanable designs, they prevent contamination, making them ideal for pharmaceutical and specialty chemical applications. A common example includes the transfer of sterile chemicals used in drug manufacturing, where maintaining purity is critical.
4. Cooling and Heating Systems Cooling and heating systems in chemical plants rely on centrifugal pumps to circulate heat transfer fluids like glycol or water efficiently. These pumps ensure consistent temperature control in reactors, heat exchangers, and condensers. For example, in polymer manufacturing, centrifugal pumps help maintain precise temperature conditions, which are crucial for achieving desired product properties.
By enabling liquid transfer, supporting critical processes, and ensuring safe handling of chemicals, centrifugal pumps have become a cornerstone for efficient operations in the chemical industry.
Selection Criteria for Centrifugal Pumps in the Chemical Industry
1. Flow Rate and Pressure Requirements Selecting the right centrifugal pump starts with evaluating flow rate and pressure requirements. Pumps must handle specific volumes and ensure consistent pressure for optimal performance. For instance, a chemical plant requiring high-volume transfer of solvents might opt for pumps capable of delivering up to 200 gallons per minute, ensuring seamless operations.
2. Material Compatibility with Specific Chemical Industry Products Material compatibility is critical to prevent corrosion and maintain safety when handling aggressive chemicals. Centrifugal pumps made from stainless steel, Hastelloy, or Teflon are often used to withstand acids, alkalis, and solvents. For example, pumps used in sulfuric acid production must resist corrosion to ensure durability and efficiency.
3. Adherence to Industry Standards (e.g., FDA, USP, GMP) Compliance with industry standards is essential for centrifugal pumps used in chemical processes. Pumps adhering to FDA, USP, or GMP regulations are mandatory for operations involving pharmaceuticals or food-grade chemicals. Such compliance ensures product quality and operational safety in regulated environments.
4. Customization Options for Unique Processes Customization options like specific impeller designs, seal types, or variable speed drives make centrifugal pumps suitable for unique chemical processes. For instance, a plant producing specialty chemicals might require pumps customized for high-viscosity fluids, ensuring efficiency and precision.
By considering flow requirements, material compatibility, regulatory compliance, and customization, chemical manufacturers can select centrifugal pumps that align perfectly with their operational needs.
Technical Specifications of Centrifugal Pumps
Capacity | 500M3 / hr |
---|---|
Head | 160mtrs |
Size | 25 to 150 |
Speed | 1400 to 2800 |
Temperature | 160 |
M.O.C. | C.I, WCB. S.S 304, S.S 316/316L Alloy-20, CD4MCU Etc. |
Best Practices for Maintaining Centrifugal Pumps
1. Regular Inspection and Cleaning SchedulesMaintaining centrifugal pumps requires regular inspections and cleaning schedules to ensure optimal performance. Routine checks help identify potential issues, such as clogged filters or leakage, before they disrupt operations. For example, setting up weekly cleaning and inspection routines ensures that pumps handling aggressive chemicals like hydrochloric acid remain in top condition.
2. Monitoring for Wear and Tear of ComponentsCentrifugal pumps should be closely monitored for wear and tear on components such as seals, bearings, and impellers. Regular monitoring can help extend the pump’s lifespan and prevent unplanned downtime. For instance, replacing worn seals promptly can prevent costly leaks and ensure the pump maintains its efficiency in critical chemical processes.
3. Proper Training for OperatorsOperator training is key to maintaining the efficiency and safety of centrifugal pumps. Ensuring operators understand the proper handling and troubleshooting of pumps reduces the risk of damage and operational disruptions. In a chemical plant, for example, trained operators can adjust pump speeds to handle varying viscosities of chemicals without affecting flow rates or causing excessive wear.
4. Upgrading Pumps to Meet Evolving Industry NeedsThe chemical industry constantly evolves, requiring centrifugal pumps to be upgraded to meet new operational demands. Upgrading pumps with modern features like energy-efficient motors or corrosion-resistant materials can boost performance and compliance. For instance, switching to pumps with energy-efficient designs can help reduce power consumption and lower operational costs in energy-intensive processes.
By following these best practices, chemical industry professionals can ensure their centrifugal pumps operate efficiently, minimizing downtime and extending equipment life.
Why Choose Our Centrifugal Pumps for Your Chemical Plant?
1. Exceptional Features of Our Centrifugal PumpsAt Jay Khodiyar, we offer high-quality centrifugal pumps designed for the chemical industry’s demanding requirements. Our pumps are engineered for efficiency, durability, and ease of use, ensuring long-term performance.
2. Customization Options for Chemical Industry NeedsWe understand that each chemical plant has unique operational needs, which is why we offer customization options for our centrifugal pumps. Whether you require specific materials, sizes, or configurations, our team works with you to provide a solution that fits your exact requirements.
3. Proven Reliability and Compliance with Industry StandardsJay Khodiyar’s centrifugal pumps are known for their proven reliability and compliance with industry standards. With over 20 years of experience, we ensure that our pumps meet quality assurance protocols like FDA, GMP, and ISO standards. This makes them ideal for handling sensitive chemicals in highly regulated environments, providing you with consistent performance and safety across your operations.
4. Exceptional Customer Support and After-Sales ServicesOur commitment to customer satisfaction goes beyond just supplying centrifugal pumps. We offer exceptional after-sales support and maintenance services to ensure your pumps run smoothly throughout their lifespan. Our team of experts is always available for troubleshooting, repair, and upgrades, ensuring that your plant operates efficiently without interruptions.
By choosing Jay Khodiyar’s centrifugal pumps, you benefit from top-notch quality, rugged construction, and unparalleled customer support, ensuring reliable and long-lasting performance for your chemical processes.
Conclusion
Centrifugal pumps are essential in the chemical industry, ensuring efficient fluid transfer and process optimization. At Jay Khodiyar, we provide high-quality, customized centrifugal pumps designed for long-lasting performance and compliance with industry standards. For reliable solutions that enhance efficiency, contact us and discover how our centrifugal pumps can elevate your operations.