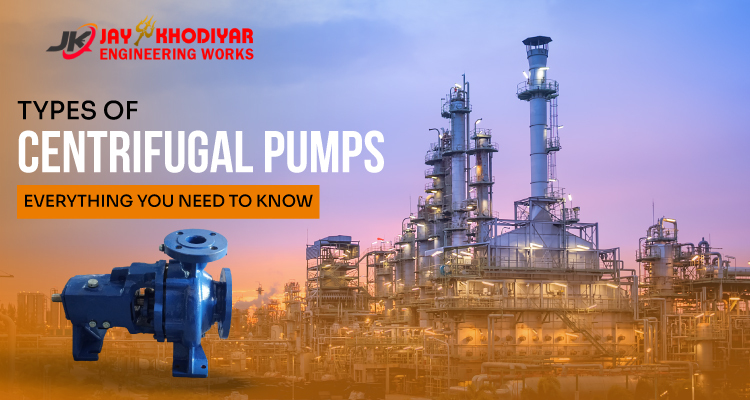
Types of Centrifugal Pumps – Everything You Need to Know
October 4, 2023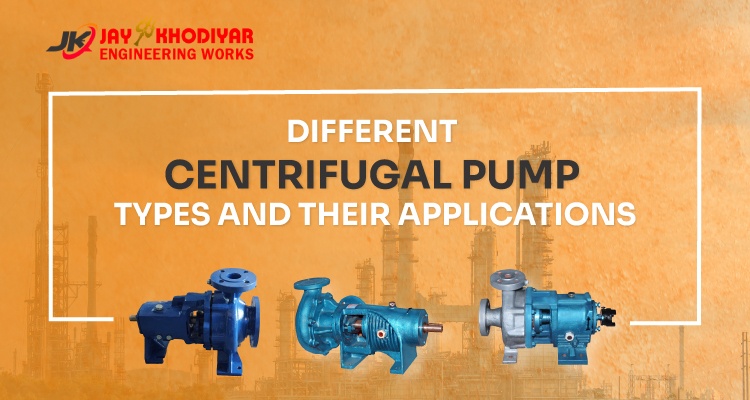
Different Centrifugal Pump Types and Their Applications
November 22, 2023Chemical pumps are an essential piece of equipment in many industries. They allow for the safe and efficient transfer of corrosive, abrasive, and other hazardous materials. Chemical pumps are designed to minimize leakage and emissions, which is important for safety and environmental reasons.
Chemical pumps can be complex and extensive equipment, so it is important to choose the right one. Depending on your specific application, it is necessary to measure all the important aspects of the pump before choosing any.
This blog is for your understanding of Chemical pumps, their applications, advantages, and what factors to consider while going for the one!
What is a Chemical Pump?
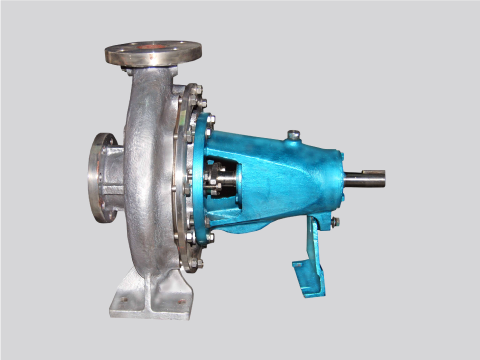
Chemical pumps are designed to be used in various industries and applications to handle and transfer chemicals and to be resistant to corrosive and abrasive liquids.
The types of chemical pumps include;
- Centrifugal pumps
- Positive displacement pumps
- Magnetic drive pumps
- Submersible pumps
The type of chemical pump that is best for a particular application depends on the specific properties of the liquid being pumped, such as its viscosity, corrosiveness, and abrasiveness.
Chemical pumps are typically made from materials that are resistant to the chemical being pumped. Common materials include stainless steel, polypropylene, and PTFE.
Chemical pumps have special features such as mechanical seals to prevent leakage and a cooling system to prevent the pump from overheating.
How Do Chemical Pumps Work?
Chemical pumps create pressure to move a liquid or chemical from one to another place. There is no established way to create this pressure, it varies on the type of chemical pump you use in your applications. More than half of the chemical pumps use impellers or rotors to create the pressure to move the liquid.
The one common type of chemical pump - Centrifugal pump uses an impeller to create a centrifugal force. Positive displacement pumps work by trapping a particular amount of liquid in a chamber and then creating a force to take it out of the chamber.
To make it easy for you to understand, here is a simplified explanation of how chemical pumps work.
- The chemical enters through the inlet port.
- The impeller rotates and flings chemicals outwards by creating a centrifugal force.
- The forced-out liquid is collected in volute casting to direct it out of the pump through the outlet port.
The speed of the impeller and the size of the volute casting determine the flow rate and pressure of the pump.
Applications of Chemical Pumps
Chemical pumps have a wide range of applications. Different industries use suitable types of pumps for their specific application or requirements.
We have listed down some common applications of Chemical pumps here:
- Chemical Manufacturing
- Water Treatment
- Cement Plants
- Paper/Pulp Production
- Mining
- Food & Beverage
- Automotive
- Oil & Gas
- Pharmaceuticals
Chemical pumps play a vital role in the production of a wide variety of products and the delivery of essential services. These and many other industries consider chemical pumps as essential equipment for their daily operations.
Advantages of Using Chemical Pumps
Chemical pumps offer numerous benefits over other chemical moving methods. They are sufficient enough to improve safety and reduce environmental impact.
Some common advantages of chemical pumps include:
- Energy Efficiency
Chemical pumps are designed to be energy efficient. It helps to save unnecessary spending on the electricity bills. Over any other pumping method, chemical pumps rank higher with their energy efficiency power.
- Corrosive Resistance
The construction of chemical pumps allows them to handle hazardous materials, such as acids, solvents, and caustics without causing any harm to the pump and environment around. With this capability, chemical manufacturers, distributors, or users can convey a variety of fluids in various conditions.
- Smooth Flow
The chemical pumps are developed to deliver a smooth and pulseless flow. The risk of damaging pipes and other equipment is reduced with the chemical pumps. These pumps avoid emissions and save manufacturers from spending extra costs on purchasing pulsation dampeners.
- Reliability & Safety
Chemical pumps are more reliable and durable. Chemical pumps are the go-to solution for the various pumping needs of many industries. These pumps have high safety standards. Chemical pumps work by serving reliability, safety, and durability. Industries can rely on chemical pumps for their long-lasting and safe operation.
- Low Maintenance
Chemical pumps are low maintenance. Pumps with high maintenance are less appealing to industries. In contrast, chemical pumps have low repair costs. With chemical pumps working by industry side, technicians can work with more focus on their operational activities, rather than looking for the pumps.
- Application Versatility
Chemical pumps serve their benefits in more than one industry. From chemical to food processing to water treatments to many other industries. Different types of chemical pumps are used in different applications to provide solutions based on specific requirements.
- Cost-efficiency
Chemical pumps are relatively cost-effective due to their low maintenance. These pumps reduce the cost of regular maintenance and repair cost. The frequency of repairing and replacing these pumps is comparatively lower than any other pumping method.
Select the Right Chemical Pump: An Ultimate Guide
The demand for chemical pumps is rapidly increasing among chemical industries. In order to protect the employees and the environment from the injurious chemicals and acids. Therefore, these manufacturers need to create a safe environment.
The use of chemical pumps differs from one to another because of the contrasting behavior of fluids. Take care of the following points before considering any chemical pump for your applications.
- Required Flow Rate
The flow rate of chemical pumps must be sufficient to meet the needs of the application. The flow rate of chemical pumps is mainly measured in gallons per minute(GPM) or liters per minute(LPM).
- Pressure Needed
The pump must be able to generate enough pressure to move the liquid through the system. The pressure is typically in pounds per square inch(PSI) or bar.
- Fluid Transfer
The chosen chemical pump should be compatible with the type of fluid being transferred. Consider the type of liquid you are moving, is it corrosive? or contains solids? Some pumps are only designed to move the acids, bases, and solvents.
- Volume of Chemical
The volume of chemicals is one important factor to consider in choosing chemical pumps. Choose a pump that can handle the required volume of chemicals without overheating.
- Application Environment
The application environment of your chemical pump is of utmost importance. Sunlight exposure on the pump, and the temperature of its installation place - keep these in mind. Do not overlook this factor because this is a definite part of the pump’s performance.
- Pump Material
The pump must be made of a material that is suitable for your application. Make sure your pump is made of stainless steel, hestelloy, and PVC. Some fluids such as acids and bases can corrode the material.
- Required Suction Lift
The suction lift is the vertical distance between the liquid level in the suction tank and the pump inlet. Choose a pump that can generate the required suction lift.
Pump Up the Performance!
Employee safety and a good environment are the top priorities for any industry, while also looking at the performance of the pump. To meet all of these, you just need to take care of the above factors or consult a reliable manufacturer of chemical pumps. If you are aligned with the second option, then we are the solution. Jay Khodiyar Pumps is the leading manufacturer of industrial pumps, supplying the pumps with the latest technology and smooth services. Pump up the performance of your business with our superior chemical pumps.