
Top 12 Industrial Pump Manufacturers in World
July 5, 2024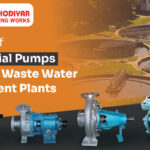
Types of Industrial Pumps Used in Wastewater Treatment Plants
July 30, 2024Introduction
Industrial operations, where precision and reliability are important – chemical pumps stand at top. These pumpsfacilitate the safe and efficient transfer of a wide range of fluids, from corrosive chemicals to volatile solvents, across various sectors including manufacturing, pharmaceuticals, and wastewater treatment.
What is a Chemical Pump & How It Works?
A chemical pump is a specialized device used primarily in industries where the handling of corrosive, abrasive, or hazardous fluids is necessary. These pumps are designed with materials and construction that ensure compatibility with the types of chemicals being transferred.
Materials such as stainless steel, alloys, and fluoropolymers (like PTFE) are commonly used due to their resistance to chemical corrosion and reactive properties. This ensures that the pump components remain intact and reliable over time, even when exposed to aggressive substances.
The working principles of chemical pumps revolve around maintaining the integrity of the fluids being transferred while ensuring operational safety. One crucial aspect is the sealing mechanism employed in these pumps. Given the potential hazards associated with chemical leaks, chemical pumps are equipped with advanced sealing technologies.
These may include mechanical seals that prevent fluid leakage by creating a barrier between moving parts, or magnetic couplings that use magnets to transmit torque through a hermetically sealed barrier, eliminating the need for conventional seals altogether.
Chemical pumps operate using various types of pump mechanisms depending on the specific requirements of the application.
Features of Chemical Pumps
Chemical pumps incorporate several key features that distinguish them from standard pumps and make them suitable for handling corrosive, abrasive, or hazardous fluids in industrial applications.
Here are some of the notable features:
1. Material Compatibility
Chemical pumps are made from materials highly resistant to corrosion and chemical reactions. Common materials include stainless steel, Hastelloy, titanium, and fluoropolymers such as PTFE. These materials ensure that the pump components can withstand the corrosive nature of the fluids being handled without degrading over time.
2. Sealing Mechanisms
To prevent leaks and ensure containment of hazardous fluids, chemical pumps utilize advanced sealing mechanisms. This may include mechanical seals, which create a barrier between the pump shaft and the housing to prevent fluid leakage, or magnetic couplings that use magnets to transmit torque through a sealed barrier without physical contact.
3. Safety Features
Chemical pumps are equipped with safety features to mitigate risks associated with handling hazardous fluids. These can include leak detection sensors that alert operators to any potential leaks or breaches in containment. Some pumps also feature double containment systems, where the pump casing has an additional layer of protection to contain leaks if the primary seal fails.
4. Corrosion Resistance
Specialized coatings and treatments are applied to internal components of chemical pumps to enhance corrosion resistance. This helps prolong the lifespan of the pump and maintain its efficiency even when exposed to aggressive chemicals.
5. Flow Control and Efficiency
Chemical pumps are designed to provide precise control over fluid flow rates and operational efficiency. They may include adjustable speed drives or variable frequency drives that allow operators to fine-tune the pump's performance according to specific process requirements.
6. Versatility in Design
Depending on the application, chemical pumps come in various designs such as centrifugal pumps, positive displacement pumps (including gear pumps and diaphragm pumps), and peristaltic pumps. Each design offers unique advantages in terms of fluid handling capabilities, pressure ranges, and viscosity compatibility.
7. Maintenance and ServiceabilityEase of maintenance is another crucial feature of chemical pumps. They are designed for easy access to internal components, facilitating routine inspection, cleaning, and repair. Manufacturers often provide maintenance guidelines and support to ensure optimal performance and longevity of the pumps.
Types of Chemical Pumps
Here are some of the common types:
1. Centrifugal Pumps
- Overview: Centrifugal pumps are widely used in chemical processing industries due to their ability to handle large volumes of fluids efficiently.
- Working Principle: These pumps use centrifugal force to impart kinetic energy to the fluid, which is then converted to pressure as it exits the impeller into the volute casing.
- Applications: Suitable for low viscosity fluids and applications where high flow rates are required. They are commonly used in chemical transfer, wastewater treatment, and cooling systems.
2. Air-Operated Double Diaphragm (AODD) Pumps:
- Overview: AODD pumps are powered by compressed air and are known for their versatility and robustness.
- Working Principle: These pumps use reciprocating diaphragms to draw and expel fluid through the pump chamber.
- Applications:
Suitable for handling corrosive, abrasive, and viscous fluids. Commonly used in chemical processing, paint manufacturing, and wastewater treatment due to their ability to handle solids and slurries.
3. Vertical Pumps:
- Overview: Vertical pumps are designed with a motor located above the liquid level, making them suitable for applications where space is limited or where fluids need to be pumped from deep wells or tanks.
- Applications: Used in sump drainage, chemical transfer from underground storage tanks, and industrial wastewater treatment where pumping efficiency and space optimization are crucial
How to Choose the Right Chemical Pump?
Here’s a guide to choosing chemical pumps for your industry:
1. Chemical Compatibility
This is perhaps the most critical factor. Different pumps are designed to handle different types of chemicals, so it's essential to check the pump's compatibility with the specific chemicals you will be handling. Ensure the pump materials (such as casing, seals, and impeller) are resistant to corrosion and can withstand the chemical properties (e.g., acidity, alkalinity, viscosity) of the fluid.
2. Pump Construction Materials
Depending on the chemicals being pumped, materials such as stainless steel, plastic (e.g., polypropylene, PVDF), or alloys may be used. Select materials that offer the required chemical resistance and durability.
3. Flow Rate and Pressure Requirements
Determine the flow rate and pressure required for your application. This will help narrow down the appropriate pump size and type (e.g., centrifugal pump, diaphragm pump) that can deliver the necessary performance.
4. Viscosity of the Fluid
Dchemicals may have high viscosity, which can affect pump performance. Certain pump types, like gear pumps or peristaltic pumps, are better suited for handling viscous fluids compared to centrifugal pumps.
5. Temperature Range
Consider the temperature range of the chemicals and the environment where the pump will operate. Ensure the pump can handle the maximum and minimum temperatures without compromising performance or safety.
6. Operational Conditions
Assess factors such as suction lift (vertical distance between pump and fluid source), discharge head (pressure needed to move fluid to desired location), and any special installation requirements (e.g., submerged installation, explosion-proof environments).
7. Maintenance and Serviceability
Evaluate ease of maintenance, availability of spare parts, and access to service support. Pumps that are easy to maintain can reduce downtime and operating costs.
8. Safety Considerations
Ensure the pump design meets safety standards and regulations for handling chemicals. This includes features like leak detection, grounding capabilities (for handling flammable liquids), and safety certifications.
9. Budget and Total Cost of Ownership
Consider both the initial purchase cost and the long-term operating costs, including energy consumption, maintenance, and replacement parts.
10. Chemical Pump Manufacturer Reputation and Support
Choose a pump from a reputable chemical pump manufacturer with a track record of producing reliable chemical handling equipment. Good manufacturer support can be invaluable for technical assistance and service.
Industrial Applications of Chemical Pump
- Chemical processing industry
- Water and wastewater treatment
- Oil and gas industry
- Paper and pulp industry
- Food and beverage industry
- Pharmaceutical and biotechnology industry
- Mining and mineral processing
- Power generation
- Textile industry
- Automotive and manufacturing
Maintenance Tips for Chemical Pumps
Look for leaks, corrosion, misalignment, and weird noises/vibrations. Record your findings for future reference.
Check oil levels, ensure proper pump-motor alignment, inspect and replace seals as needed, and test pressure relief valves according to instructions.
Track flow rate, pressure, and power consumption to identify potential issues early on.
Refer to the manufacturer's guide for specific maintenance procedures and recommended parts.
Develop a regular maintenance schedule and train personnel in safe handling and maintenance practices.
Leading Chemical Pump Manufacturer in India – Jay Khodiyar Pumps
We almost have covered everything essential about chemical process pumps – from their features and working principles to different types and applications. One thing that is left is – where should you get it from, and the answer is simple – Jay Khodiyar Pumps.
Jay Khodiyar Pumps is a leading chemical pump manufacturer in India, offering a diverse range of chemical process pumps with great efficiency. Trust Jay Khodiyar Pumps for your chemical pump needs.