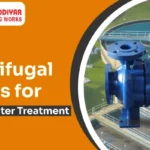
Centrifugal Pump for Waste-Water Treatment
January 30, 2025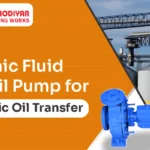
Thermic Fluid Hot Oil Pump for Synthetic Oil Transfer
February 3, 2025What is a Closed Impeller Centrifugal Pump?
A closed impeller centrifugal pump is a type of industrial centrifugal pump where the impeller is fully enclosed between two cover plates. This design enhances efficiency, minimizes internal fluid recirculation, and minimizes wear, making it ideal for applications that require high-efficiency centrifugal pumps. These pumps are widely used in chemical processing, water treatment, HVAC systems, and manufacturing industries where consistent performance is crucial.
How Does a Closed Impeller Centrifugal Pump Work?
A closed impeller centrifugal pump operates using centrifugal force to efficiently transfer fluids. When powered, the motor drives the impeller, creating a low-pressure zone at the suction inlet, which allows fluid to enter the pump smoothly.
As the fluid moves through the enclosed impeller, centrifugal force pushes it outward through the impeller vanes, increasing its velocity. The pump casing then directs this high-speed fluid, converting kinetic energy into pressure energy for effective discharge.
The closed impeller design reduces internal recirculation, enhances pump efficiency, and minimizes wear. This makes it ideal for applications requiring high-pressure fluid handling, such as chemical processing, water treatment, and industrial systems.
Key Components of a Closed Impeller Pump
A closed impeller centrifugal pump is made up of important parts that work together to move fluids efficiently. Each component plays a key role in ensuring smooth operation, durability, and high performance. Knowing these parts helps in choosing the right pump and keeping it well-maintained.
1. Impeller
The impeller is the core component that generates centrifugal force to move the fluid. In a closed impeller design, it is enclosed between two plates, which enhances efficiency by reducing fluid recirculation and minimizing wear.
2. Pump Casing
The pump casing encloses the impeller and directs the fluid flow. It also protects internal components from external damage and helps maintain consistent pressure within the pump.
3. Suction Inlet and Discharge Outlet
The suction inlet allows fluid to enter the pump, while the discharge outlet directs the pressurized fluid out. Their design influences the pump's efficiency and flow rate.
4. Motor
The motor provides the mechanical energy needed to drive the impeller. It plays a crucial role in determining the pump’s speed, efficiency, and overall performance.
5. Shaft and Bearings
The shaft connects the motor to the impeller, ensuring rotation. Bearings support the shaft, reducing friction and wear to maintain smooth operation over time.
6. Seals and Gaskets
Seals and gaskets prevent fluid leakage and help maintain pressure. Proper sealing ensures operational reliability and extends the pump’s lifespan.
Closed vs. Open Impeller: What’s the Difference?
Closed impeller centrifugal pumps have an enclosed design with two plates surrounding the vanes, improving efficiency and reducing fluid loss. This structure makes them ideal for applications requiring high pressure and clean fluid handling. The enclosed vanes also minimize internal recirculation, leading to better energy efficiency and a longer lifespan.
On the other hand, open impeller pumps have exposed vanes without enclosing plates, making them better suited for handling fluids containing solids or debris. Their open design allows easy cleaning and maintenance, but they tend to be less efficient due to higher fluid recirculation. Additionally, open impellers may experience more wear and tear over time, requiring frequent inspections and replacements.
The choice between closed and open impellers depends on the application. If high efficiency and pressure handling are needed for clean fluids, a closed impeller is the best option. However, if the fluid contains solids or requires easier maintenance, an open impeller pump may be more suitable. Understanding these differences helps industries select the right pump for their specific needs.
The comparison table can make this clearer:
Feature | Closed Impeller | Open Impeller |
---|---|---|
Efficiency | High | Moderate |
Fluid Type | Clean liquids | Solids/slurries |
Maintenance | Less frequent | Frequent |
Wear & Tear | Low | High |
Best Use | High-pressure, clean applications | Dirty fluids, easy cleaning |
Advantages of Using a Closed Impeller Centrifugal Pump
A closed impeller centrifugal pump offers several benefits, making it a preferred choice for industries needing efficient and reliable fluid movement. Its enclosed design improves performance, reduces wear, and lowers maintenance needs, ensuring long-term cost savings.
- Higher Efficiency – Reduces internal leakage and increases energy efficiency.
- Longer Lifespan – Less wear and tear due to enclosed impeller design.
- Better Handling of Clean Fluids – Ideal for applications requiring smooth fluid movement.
- Reduced Maintenance – Fewer chances of clogging and damage.
- Lower Operational Costs – Less energy consumption compared to open impeller pumps.
Best Applications of Closed Impeller Pumps
Closed impeller centrifugal pumps are widely used in various industries due to their efficiency and durability. Some of the best applications include:
- Chemical Processing Plants – Handling corrosive and non-corrosive liquids.
- Water Treatment Facilities – Used in filtration and distribution systems.
- Food and Beverage Industry – For transferring clean liquids in production lines.
- Pharmaceutical Industry – Used in sanitary and precision fluid applications.
- HVAC Systems – Circulating fluids in heating and cooling systems.
Factors to Consider When Choosing a Closed Impeller Pump
When selecting a closed impeller centrifugal pump, consider the following factors:
-
1. Flow Rate and Head – Choose a pump that meets your pressure and volume requirements.
- 2. Material of Construction – Stainless steel, bronze, or other corrosion-resistant materials for durability.
- 3. Efficiency – Look for high-efficiency models to save energy.
- 4. Compatibility with Fluids – Ensure the pump material is suitable for the liquid being pumped.
- 5. Operating Temperature and Pressure – Select a pump that can handle the specific conditions of your application.
- 6. Maintenance Requirements – Consider ease of maintenance and availability of spare parts.
Maintenance Tips for Longer Pump Life
Proper maintenance can extend the life of your closed impeller centrifugal pump. Follow these essential tips:
- Regular Inspection – Check for leaks, vibrations, and unusual noises.
- Lubrication – Keep bearings well-lubricated to avoid wear and tear.
- Cleaning – Prevent buildup of sediments and debris inside the pump.
- Seal and Gasket Checks – Replace worn-out seals to prevent leaks.
- Monitor Performance – Track flow rates and pressure levels to detect inefficiencies early.
Common Issues and Troubleshooting in Closed Impeller Pumps
Even high-quality closed impeller centrifugal pumps can face performance issues over time. Identifying problems early and applying the right fixes can prevent downtime, reduce repair costs, and extend pump life. Here are some common issues and their solutions.
Problem | Possible Cause | Solution |
---|---|---|
Low Flow Rate | Clogged impeller or worn-out components | Clean or replace the impeller |
Excessive Noise | Cavitation or misalignment | Check for air pockets and realign the pump |
Overheating | Insufficient lubrication or blocked cooling passages | Ensure proper lubrication and clear blockages |
Leakage | Worn-out seals or gaskets | Replace seals and tighten fittings |
Vibration | Unbalanced impeller or misalignment | Inspect and balance the impeller |
Why Choose a Closed Impeller Centrifugal Pump?
A closed impeller centrifugal pump is the preferred choice for industries requiring high-efficiency, reliability, and long-term durability. Its enclosed design ensures superior fluid handling, reduced operational costs, and minimal maintenance. Top-quality industrial pumps with closed impellers provide excellent performance in applications requiring precise fluid control.
Conclusion
Closed impeller centrifugal pumps provide high efficiency, durability, and reliable performance for industries that require smooth and consistent fluid flow under high pressure. Their enclosed design minimizes wear, enhances energy efficiency, and extends pump life. With proper maintenance, they offer long-term value and cost savings.
Selecting the right pump depends on flow rate, pressure, and material compatibility. At Jay Khodiyar, we specialize in high-quality closed impeller centrifugal pumps built for industrial applications. Explore our product range or Contact us for expert assistance in choosing the perfect pump for your needs.