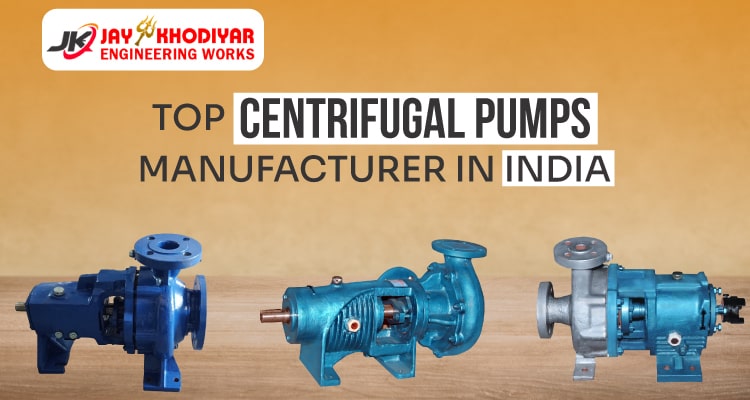
Top Centrifugal Pumps Manufacturer in India
January 30, 2024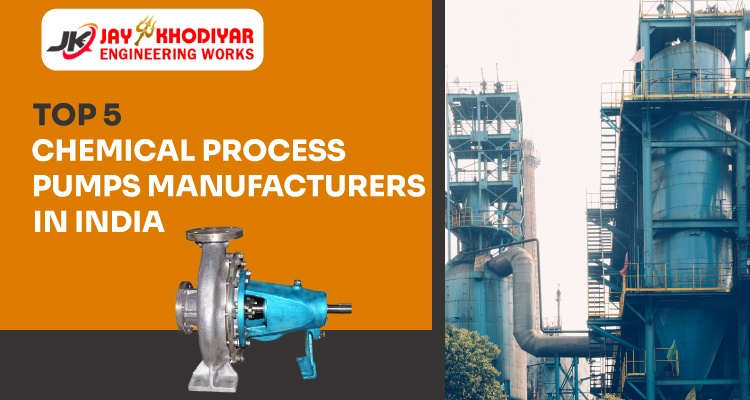
Top 5 Chemical Process Pumps Manufacturers in India
March 8, 2024If you’re working in the pharmaceutical industry, you must rely heavily on pumps for efficiently producing and processing pharmaceutical drugs and medicines.
As you may already know, pumps allow you to precisely control the flow, transfer, mixing, and dosing of liquids, gases, powders, and slurries.
This blog post will provide you with an overview of the major types of pumps used in pharmaceutical manufacturing processes and their key applications.
Centrifugal Pumps
Centrifugal pumps are one of the most common types you will find in pharmaceutical processes. These pumps use an impeller to accelerate fluids and build up a centrifugal force that pushes the fluid out of the pump.
Centrifugal pumps are great for transferring large volumes of low-viscosity fluids and materials. You can use them for applications like transferring raw materials, solvents, and finished products between vessels in your facility.
The benefits of centrifugal pumps are high flow rate, low cost, and easy maintenance. Their main limitation is that they are not suitable for handling high-viscosity fluids
Some examples of centrifugal pump types commonly used in pharmaceutical applications are overhung pumps, axial split case pumps, vertical inline pumps, and self-priming pumps.
Lift Pumps
Lift pumps are used to push liquids from a lower to higher elevation.
For the uninitiated, they are vertical pumps that must overcome the static lift to transfer fluids uphill against gravity. Types of lift pumps include submersible, sump, and vertical turbine pumps.
In pharmaceutical plants, lift pumps are used to transfer liquids between vessels and storage tanks at different floor levels. They efficiently move large volumes of water, solvents, and in-process fluids between low and high elevations.
In short, Lift pumps provide reliable transfer while minimizing shear and maintaining fluid integrity.
Booster Pumps
Booster pumps increase fluid pressure in pipelines transporting liquids over long distances. They are installed when fluids must be pumped to remote areas at higher elevations.
In pharmaceutical plants, booster pumps maintain a constant pressure for the supply of steam, water, and heat transfer fluids to various processes.
They compensate for pressure drops in extensive piping networks. Booster pumps also increase water pressure for effective cleaning and sanitization operations. Reliable booster pumps are critical to ensure fluids reach all points of use with adequate pressure.
Arterial Pumps
Arterial pumps are used in pharmaceutical waste management systems.
They are heavy-duty and can pump a wide variety of solids, slurries, and viscous liquids. The screw design provides an uniform flow rate and gentle pumping action.
Furthermore, Arterial pumps have large pump heads to handle solid particles without clogging. They can efficiently transfer corrosive chemicals, wastewater, sludge, and pharmaceutical residues over long distances.
Not just that but the ease of maintenance, durability, and long service life make them suitable for continuous pharmaceutical waste transfer duties.
Positive Displacement Pumps
Positive displacement pumps work in a different way than centrifugal pumps. They move liquids by first trapping a set amount of the liquid. Then they force that trapped amount into the output pipe.
These pumps allow you to precisely control the flow rate regardless of back pressure. This makes them ideal for metering and dosing applications where accuracy is critical.
Some types of positive displacement pumps used are piston pumps, diaphragm pumps, peristaltic pumps, and rotary lobe pumps.
The benefits of positive displacement pumps are the ability to handle high-viscosity fluids, good suction lift, reversible flow, and high precision. On the other hand, these pumps have some drawbacks as well. The main drawbacks are the pulsatile flow they produce, low flow rates, and high costs.
Usually, positive displacement pumps are used to transfer viscous liquids, precisely dosing chemicals and ingredients, and accurately meet small ingredient quantities.
Lobe Pumps
Lobe pumps are external gear rotary pumps used for viscous liquids like gels, and creams. .
The pumping action is gentle and ideal for shear-sensitive pharmaceuticals. They are self-priming, can run dry, and handle solids.
Generally, Lobe pumps are used for transferring, dosing, and filling high-viscosity pharmaceuticals like ointments, syrups, and gels. They provide smooth, pulsation-free flow crucial for fragile pharmaceutical products.
Overall, Lobe pumps enable accurate, gentle, and hygienic handling of viscous pharmaceutical formulations.
Diaphragm Pumps
Diaphragm pumps are used for corrosive, abrasive, and viscous liquids.
The diaphragm provides isolation between the fluid and pump internals. This allows the pumping of hazardous and toxic materials safely. They are ideal for metering and transferring corrosive ingredients in pharmaceuticals.
Moreover, Diaphragm pumps also prevent cross-contamination and product degradation with their seal-less design. They provide low-shear, gentle pumping action crucial for shear-sensitive drugs and formulations.
Vacuum Pumps
On top of centrifugal and positive displacement pumps, the pharmaceutical industry also uses vacuum pumps from time to time. .
These pumps are used to create suction to efficiently remove air, gases, or vapors from vessels, reactors, condensers, and transfer lines. Furthermore, they also help maintain the vacuum conditions necessary for many important pharmaceutical processes like distillation, drying, freeze drying, and solvent recovery.
Common types of vacuum pumps are liquid ring, dry claw, rotary vane, reciprocating, scroll, and diaphragm pumps. The benefits of using these pumps include suitability for handling toxic, explosive, and heat-sensitive materials.
As for the use case, vacuum pumps are mainly used for achieving vacuum in reactors, condensers, centrifuges, filtration systems, and other vessels.
Industrial Chemical Pumps
These pumps are designed for hazardous chemical transfer and processing. They provide safe containment and transfer of toxic, flammable, and reactive chemicals via their leak-proof construction.
Materials like stainless steel, PTFE, carbon, and alloys resist corrosion from acids, caustics, and solvents.
What’s more is that Industrial chemical pumps safeguard personnel while efficiently handling large capacities of hazardous pharmaceutical chemicals and intermediates.
Overall, the robustness and reliability of industrial chemical pumps help meet stringent safety requirements.
Conclusion
Efficient and reliable pumps are crucial equipment for pharmaceutical manufacturing. As we reviewed, various types like centrifugal, positive displacement, and vacuum pumps are used across pharmaceutical processes.
These pumps enable the safe, hygienic, and controlled transfer, dosing, mixing, and processing of pharmaceutical raw materials, intermediates, and finished products.
That said, if you’re looking for a trustworthy and reliable pump manufacturer, Jay Khodiyar Pumps can help.
We have over 25 years of experience supplying high-quality pumps precisely engineered for pharmaceutical industry applications. Our expertise ensures you get the right pump for your specific needs whether it's sterile transfer, precise metering, or achieving a reliable vacuum.
So for your critical pharmaceutical pumping needs, you can trust Jay Khodiyar Pumps to deliver pumps that enhance your productivity and peace of mind.