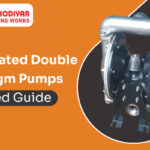
Air Operated Double Diaphragm Pumps – A Detailed Guide
August 27, 2024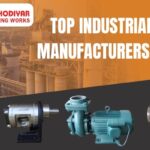
Top Industrial Pump Manufacturers in USA
September 20, 2024Industrial pumps never failed to ensure the safety and efficient handling of various chemicals in the chemical industry. These pumps are designed to handle a wide range of chemicals, from corrosive liquids to highly viscous substances.
The type of chemical pumps used in the chemical industry depends on several factors, including fluid’s properties, the desired flow rate, and more.
In this blog, you’ll get to know about the major types of industrial pumps used in the chemical industry, how they work, and more.
Top 4 Pumps Used in the Chemical Industry
The chemical industry heavily relies on industrial pumps to transfer fluids between processes, storage tanks, and transportation vessels. Here is main 4 pumps used in this industry:
1. Centrifugal Pumps
A centrifugal pump is a type of dynamic pump that uses rotational energy to move fluids. Centrifugal pumps are widely used in the chemical industry due to their ability to handle various fluids and adaptability to different operational conditions.
They are employed for transferring chemicals, processing fluids, and slurries between tanks, reactors, and other equipment. Their high flow rates and reliable performance make them ideal for continuous processes.
In chemical plants, centrifugal pumps are often used to handle corrosive, abrasive, and hazardous chemicals. Specialized materials and designs are employed to handle these challenging fluids.
How Do They Work?
Centrifugal pumps operate on the principle of centrifugal force. They consist of a rotating impeller enclosed in a casing. As the impeller spins, it creates a centrifugal force that pushes the fluid outward from the center of the impeller. This action increases the fluid's velocity and pressure, forcing it to flow through the pump and into the discharge pipe.
Features
- Highly Versatile
- Energy Efficient
- Heavy Duty Design
- Low Maintenance
- High Operating Reliability
- Safe Fluid Handling
- High Productivity
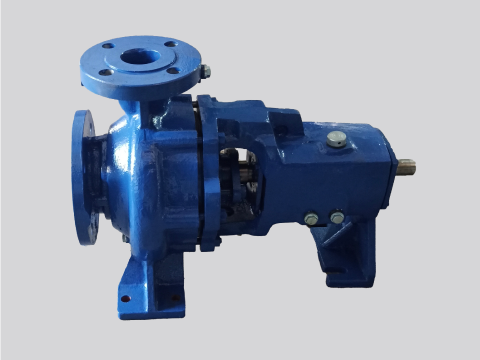
Centrifugal Pump
2. Chemical Pump
Chemical pumps are specifically designed to handle and transfer chemicals, which can often be corrosive, abrasive, or hazardous. These pumps are specifically engineered to meet the demanding requirements of chemical processes, ensuring safe and efficient transfer of chemicals.
Chemical pumps are made from materials resistant to corrosion caused by aggressive chemicals, such as acids, alkalis, and solvents. They can operate in a wide range of temperatures, from extremely cold to high-temperature environments.
How Do They Work?
Chemical pumps work by utilizing various mechanical principles to move fluids from one point to another. Centrifugal pumps use centrifugal force to increase the fluid's velocity and pressure, while positive displacement pumps trap and force a fixed volume of fluid forward.
Features
- High-Efficiency Rate
- Low Power Consumption
- Durable
- Easy To Install
- Low Maintenance
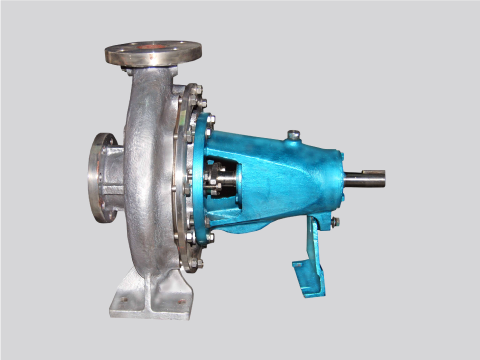
Chemical Pump
3. Monoblock Pump
Monoblock pumps are a popular choice in the chemical industry due to their compact design, reliability, and ease of maintenance. These pumps consist of a single-stage centrifugal pump and a directly coupled electric motor, all housed within a single casing.
Monoblock pumps can handle a variety of chemicals, from corrosive liquids to viscous substances. They are often more cost-effective than other pump types due to their simplicity and reduced maintenance requirements.
How Do They Work?
Monoblock pumps work by utilizing centrifugal force to move fluids. The pump's electric motor drives a rotating impeller, which creates a centrifugal force that pushes the fluid outward from the center of the impeller. This action increases the fluid's pressure and velocity, forcing it to flow through the pump and out the discharge port. The compact design of Monoblock pumps eliminates the need for separate couplings between the pump and motor, improving efficiency and reducing the risk of leaks.
Features
- Rugged Design
- Superior Performance
- Durability
- Cost Saving
- Increased Productivity
- Easy Maintenance
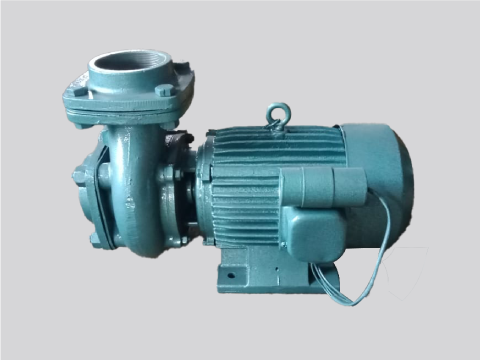
Monoblock Pump
4. Polypropylene Pump
Polypropylene pumps are a versatile and reliable choice in the chemical industry, renowned for their exceptional chemical resistance and durability. Constructed from polypropylene, a thermoplastic polymer known for its resilience against a wide range of chemicals, these pumps are ideal for handling corrosive and aggressive fluids.
Polypropylene pumps are lightweight, making them easy to install and transport. Polypropylene is a non-toxic material, making it suitable for applications where contamination must be avoided. These are generally more cost-effective than pumps made from other materials, such as metals.
How Do They Work?
Polypropylene pumps operate on the same principles as other centrifugal pumps. The impeller, a rotating disk with vanes, spins inside a casing. As the impeller rotates, it creates a centrifugal force that pushes the fluid outward from the center of the impeller. This action increases the fluid's velocity and pressure, forcing it to flow through the pump and into the discharge pipe.
Features
- Easy Maintenance
- Strong Construction
- Leak Proof
- Efficient Design
- Corrosion Resistant
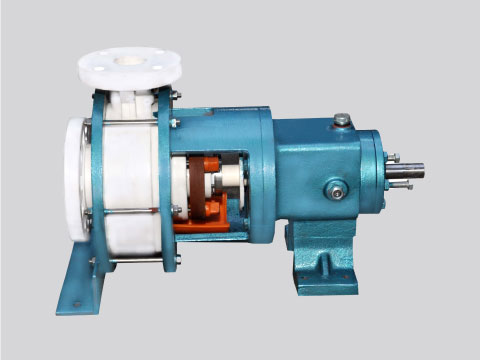
Polypropylene Pump
Conclusion
The chemical industry always demands precision with effectiveness, as the risks involved in it are comparatively higher. Therefore, it is important we incorporate the right pumps when it comes to chemical industry.
Jay Khodiyar Engineering is a leading manufacturer of high-quality industrial pumps, specialized in the chemical industry. With years of experience and expertise in the industry, we offer a range of industrial pumps to meet the specific needs of your chemical operations.
Experience the difference with our industrial pumping solution.